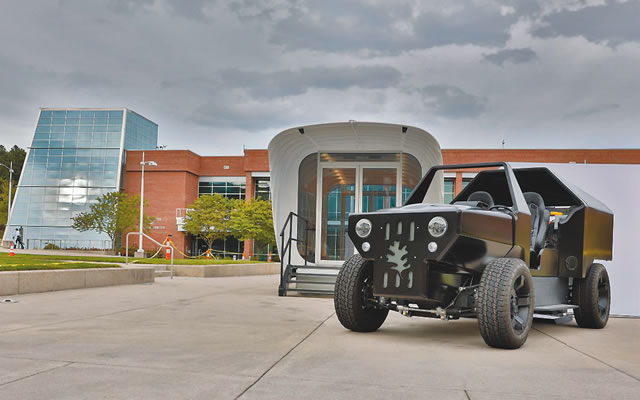
The automobile world is getting more excitingly high-tech by the day as automakers continue to research into new technological designs of bringing something novel to the table, all in a bid to beat competition and remain a force to reckon with in the industry.
There have been talks about self-driving cars, which are meant to arguably address the problem of distracted driving, reduce auto crashes and more. A number of automakers are also working on vehicles that can operate on the highway, in the air as well as sail well in the river/ocean, depending on the terrain the users find themslves.
The latest innovation is coming from the United States where a 3-dimentional Printed Utility Vehicle created by the state’s Department of Energy has been unveiled to power any home completely wireless.
The PUV can be powered by a solar 3D-printed home, or send power to the home through vehicle-to-grid charging. It can use an electric-hybrid propulsion system, with a range-extending compressed natural gas generator, according to its maker.
The vehicle can send energy to or from a house completely wirelessly, according to the report. “This is one instance that our phones could learn a little something from a car, rather than the other way around,” it adds.
An online auto journal, Auto Blog, says the advanced vehicle is printed from plastic that is similar to what is used in Lego bricks, “but it has been reinforced by adding some carbon fibre to the mix.”
A few days ago, a translogic host, Jonathon Buckley, headed to the Oak Ridge National Laboratory in Tennessee to drive the new vehicle and learn more about the solar-powered home that was developed with it.
Although the cost of the vehicle has not been disclosed, its maker says it is ready to produce on request and ship to anywhere it will be needed. This should interest some Nigerians who can afford the PUV, where electricity from the national grid has remained appallingly erratic.
The introduction of the vehicle is coming about two years after the production of the first 3-dimentional printed car in Chicago by Local Motors.
The Strati, named after the Italian word for layer, was printed in one piece over 44 hours using a process called direct digital manufacturing — the seamless fabrication of components from computer design to physical object.
A report online by Scientific America said, “Mechanical components of the vehicle, including the battery, motor and suspension, were obtained from various sources, such as Renault’s urban electric car Twizy.”
It quoted the Chief Executive Officer, Local Motors, John Rogers, as saying that the Strati marked a breakthrough in the automotive history by proving that a car could be created in an entirely new way.
“Our whole bet has been for the military or average civilian consumers or for fleet customers, that if you can change the way you make a vehicle, and do it faster, then you can catch innovation as it comes along more quickly,” he said.
The report said the Strati, considered a two-seater ‘neighborhood’ electric vehicle, had a range of 100 to 120 miles (depending on the battery pack) and a maximum speed of 40 mph.
“But perhaps more novel than the Strati itself is the way in which it was made. Rapid, local, flexible manufacturing could have broad economic, societal and environmental implications,” it stated.
Interestingly, Local Motors, best known for making the Rally Fighter off-highway vehicle, was reported to have signed a partnership agreement with the Department of Energy’s Oak Ridge National Laboratory in January 2013 when the auto firm did not have a printing machine; no printing material and did not have a design for the car.
“All of those tasks were completed in just six months,” the report stated.
For Rogers, the ability to make locally is the ability to innovate locally. These innovations could then work their way up the production chain to reach a mass scale.
“The design for the Strati, for instance, was selected from more than 200 entries submitted by Local Motors’ online community. Local Motors decided to go with an electric powertrain because it has fewer parts and so is relatively simple to construct.
The open-source platform was the core of Local Motors’ projects. And later, other automakers started to embrace the concept.
In March 2014, General Electric Co. announced a partnership with Local Motors to build and commercialize next-generation GE products using Local Motors’ First Build open-source platform. GE is also a strong supporter of 3-D printing, with more than 300 printers currently in use across the company.
The ability to make complex shapes using fewer parts and less material without sacrificing strength is one of the main benefits of 3-D printing, according to Anthony Vicari, a research associate at Lux Research and author of a recent 3-D printing market report.
He added that lighter-weight designs would usually have direct energy-saving benefits for the aerospace and automotive industries in terms of reduced fuel burn.
0 comments:
Post a Comment
ff on Twitter: @TheNaijaInfo
Facebook.com/NaijaInfo
Email: TheNaijaInfo@gmail.com
What do you think about this post?